The Knowledge Bottleneck in Chemistry: Why Sharing Skills Is So Hard - And What We Can Do About It
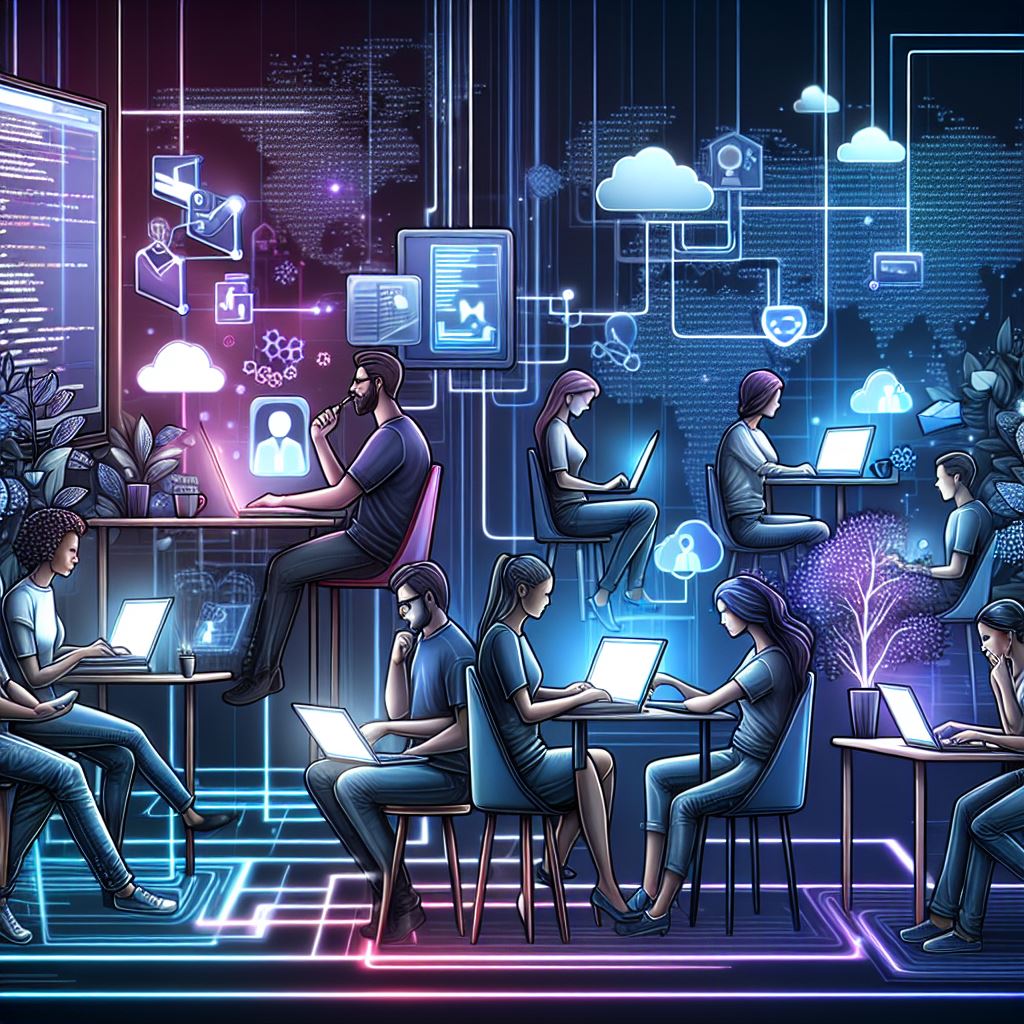
The Knowledge Bottleneck in Chemistry: Why Capturing and Transferring Knowledge Is So Hard
In the scientific world, innovation moves fast - but knowledge doesn’t always keep up. Whether it’s onboarding new chemists, scaling teams across geographies, or transitioning from legacy systems to new, capturing and transferring knowledge remains one of the most persistent challenges in the industry - whether between departments or across entire organizations.
In today’s fast-paced, knowledge-driven economy, scientific organizations are only as strong as the collective expertise of their people.
Why Is It So Difficult?
Despite the abundance of tools and management tactics designed to facilitate knowledge sharing, the process remains stubbornly complex. Here’s why:
1. Tacit Knowledge Is Hard to Document, Sometimes ItLives in Lab Books But Most Of The Time It Lives In People!
Much of the most valuable knowledge in chemistry isn’t written down. It’s embedded in synthetic decisions, previous experience and knowledge, and the mental models of experienced chemists. Chemistry is a heavily manual and practical science after all, which means that most knowledge is gained through experience, intuition, and context.
This kind of knowledge is difficult to articulate, let alone document in a way that others can easily absorb.
This makes it hard to transfer, especially when people leave or teams reorganize.
2. Experimentation Sometimes Outpaces Documentation
The average chemist will setup 1-2 experiments a day, or more if they are screening conditions or creating libraries. The reality of the heavy manual nature of the job means that sometimes it’s faster to just do, than spend the time documenting every decision and thought. Lab books, even when heavily used, are often incomplete and outdated and the information quality of what is captured varies from chemist to chemist. Chemists are left relying on memory, or reverse-engineering past decisions. This leads to a lot of bias while limiting innovation too. It's faster after all to do the same as before, than to figure things out or try new chemistry.
3. Silos Still Exist And Silos Are Specialised
Departments often operate in isolation, with their own language, tools, and priorities. Differences in chemistry specialisation or processes, like R&D and manufacture, or medicinal chemistry and formulation, can often lead to communication gaps, even within the same organisation. This creates barriers to knowledge flow, even when the intent to collaborate is there.
4. Time Constraints
Employees are busy and productivity in the chemical sector is already low. Taking time to document processes, mentor others, or contribute to knowledge bases often falls to the bottom of the priority list - especiallywhen it’s not directly tied to performance metrics.
5. Lack of Incentives
Without clear incentives or recognition, there’s little motivation for individuals to share what they know. Knowledge hoarding can even be seen as a form of job security. The phenomenon of the "golden hands", the one chemist that can execute this reaction better than anyone else is a very common manifestation of knowledge hoarding. This limits innovation and creates organisations that lack practical ownership of their IP.
6. Generic Technology Isn’t a Silver Bullet
While platforms like chat bots, wikis, intranets, ELNs and collaboration tools are helpful, they’re only as effective as the generic models that created them, as well as the culture and processes that support them since their input relies entirely on the user.
What Can Be Done?
To overcome these challenges, organizations need to take a strategic and human-centered approach:
- Foster a culture of learning and sharing by investing in chemists and upskilling them.
- Invest in specialised technology designed specifically for the job, it is a complex one afterall.
- Make standardisation and knowledge capture part of the workflow, without relying on user input.
- Bridge the silos between chemistry specialisations, sites and organisations by utilising the common ground, we are all chemists at the end of the day.
Final Thoughts
Knowledge is one of the most valuable assets an organization has - but only if it is captured and owned. The organizations that thrive in the future will be those that treat knowledge capture and transfer not as a one-time task, but as a continuous, strategic priority.
Want further inspiration? Ask for a demo of our platform to see how we achieved this.
Other articles
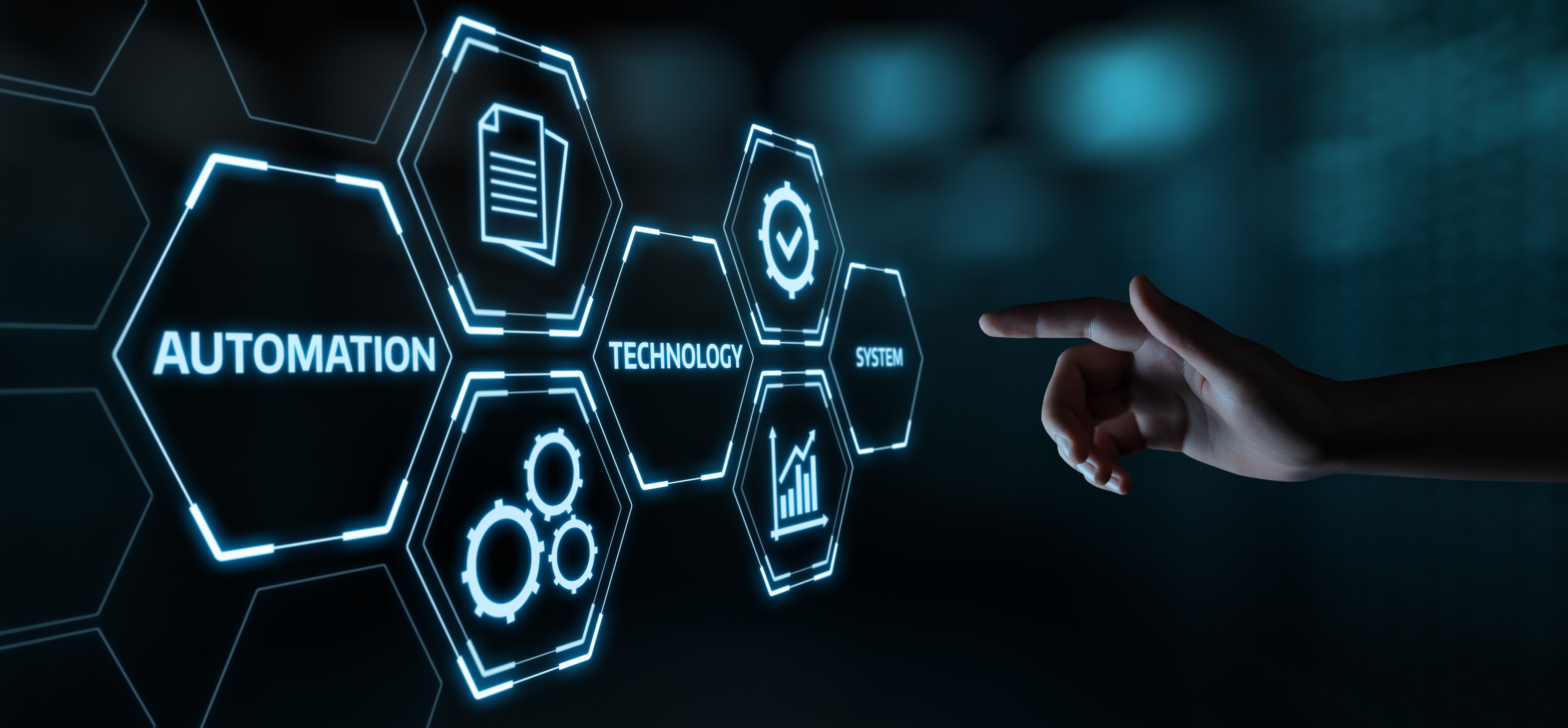
Not all automation is equal
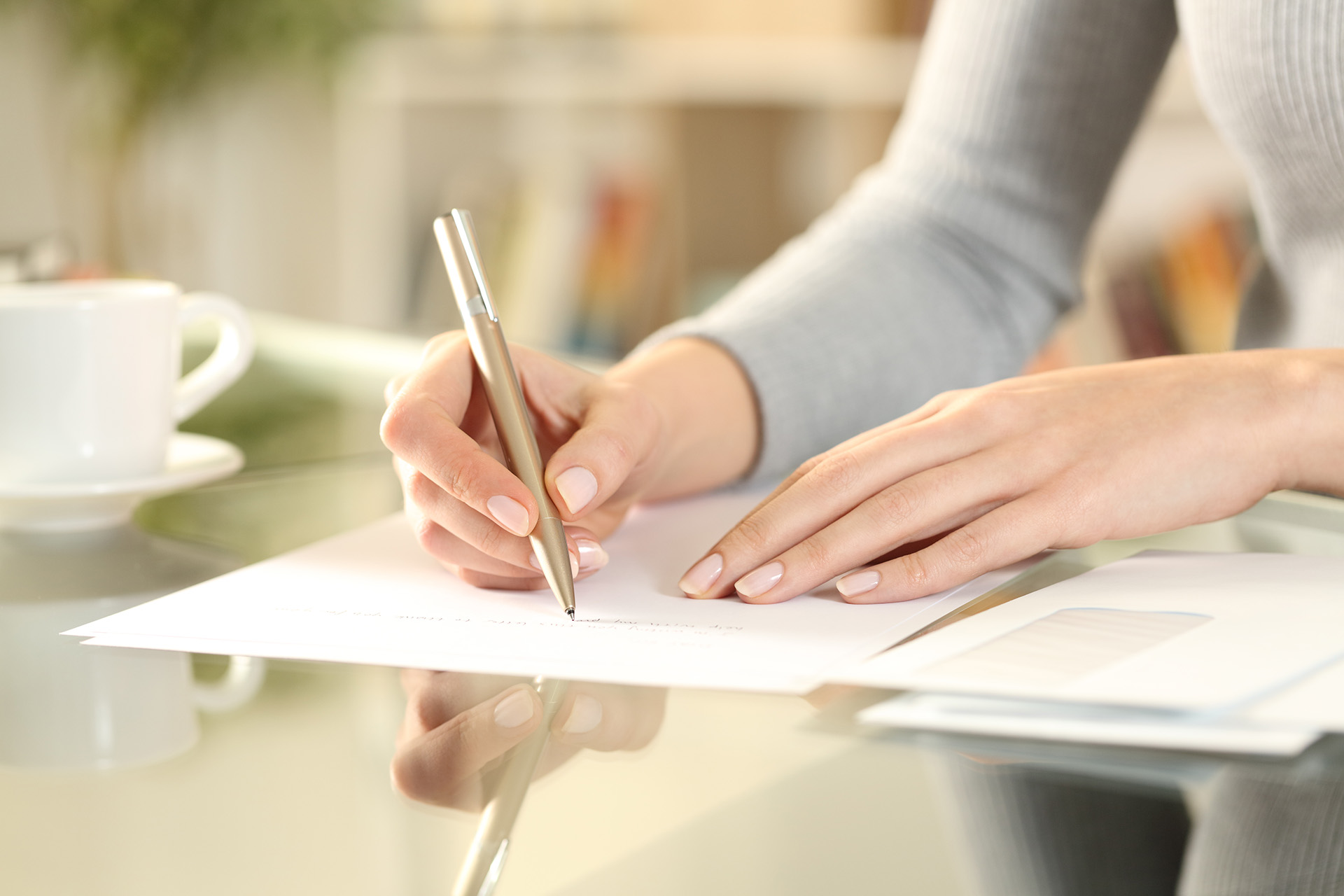
A Letter to Chemistry
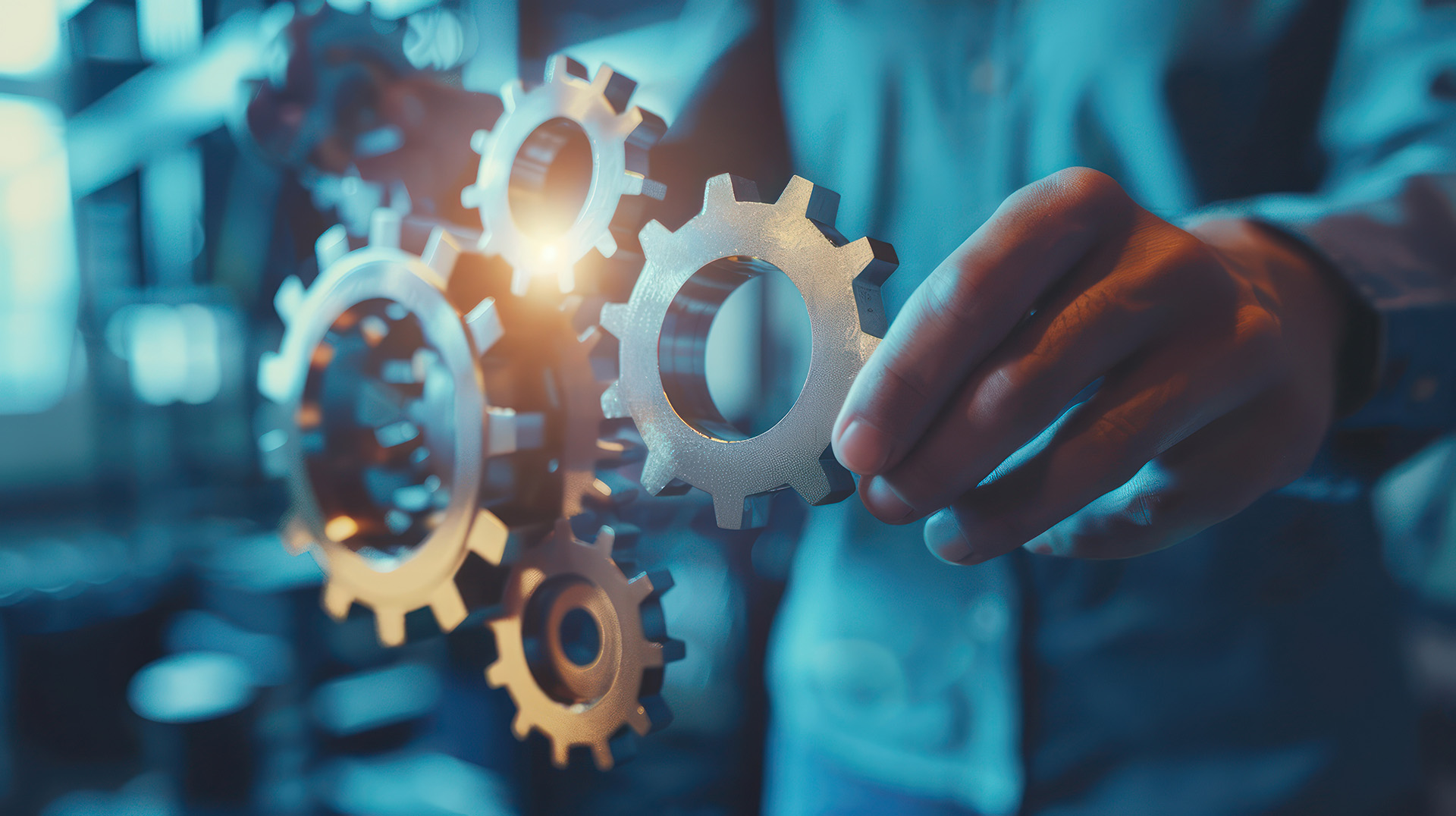
The Value Proposition of Automation
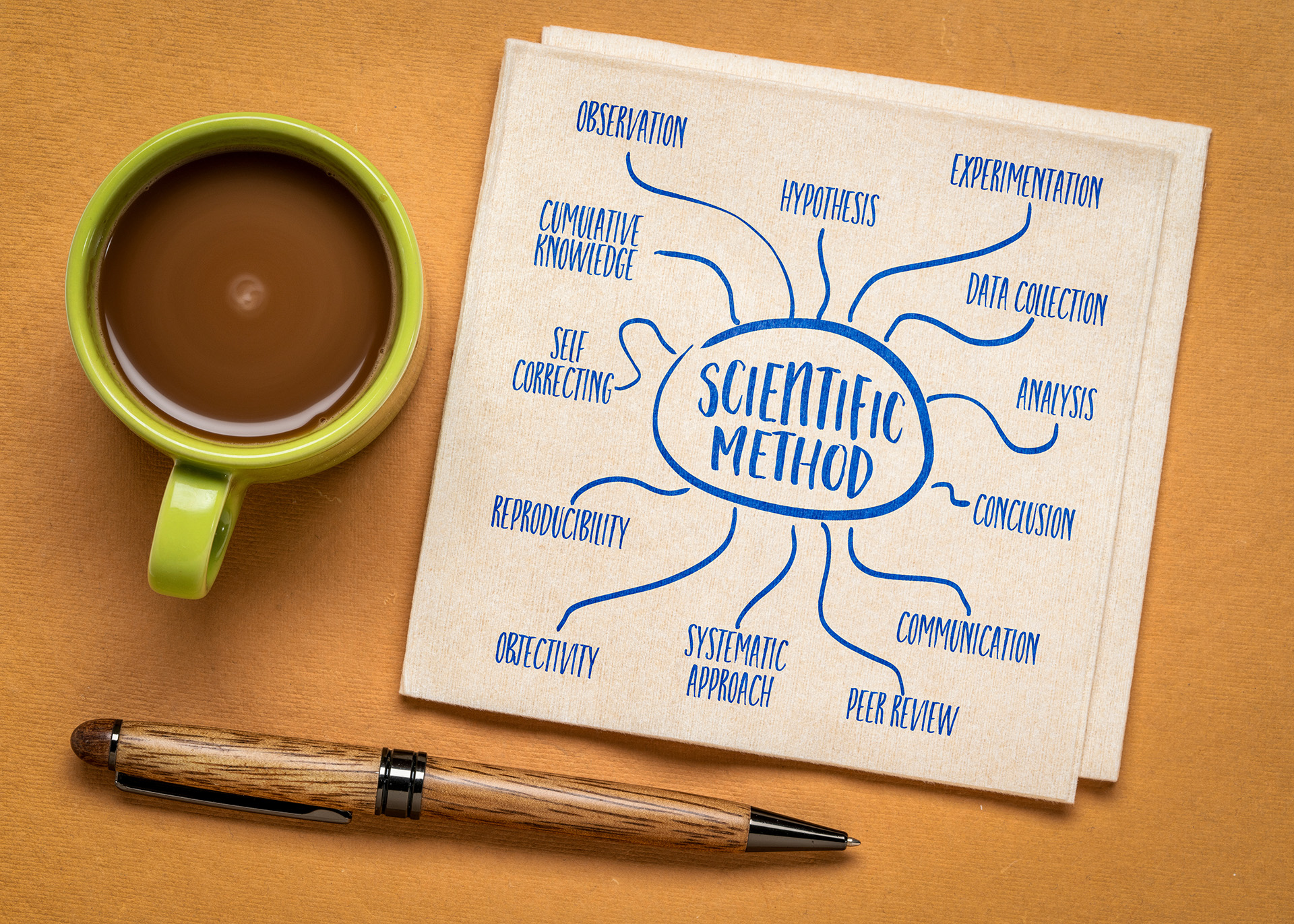